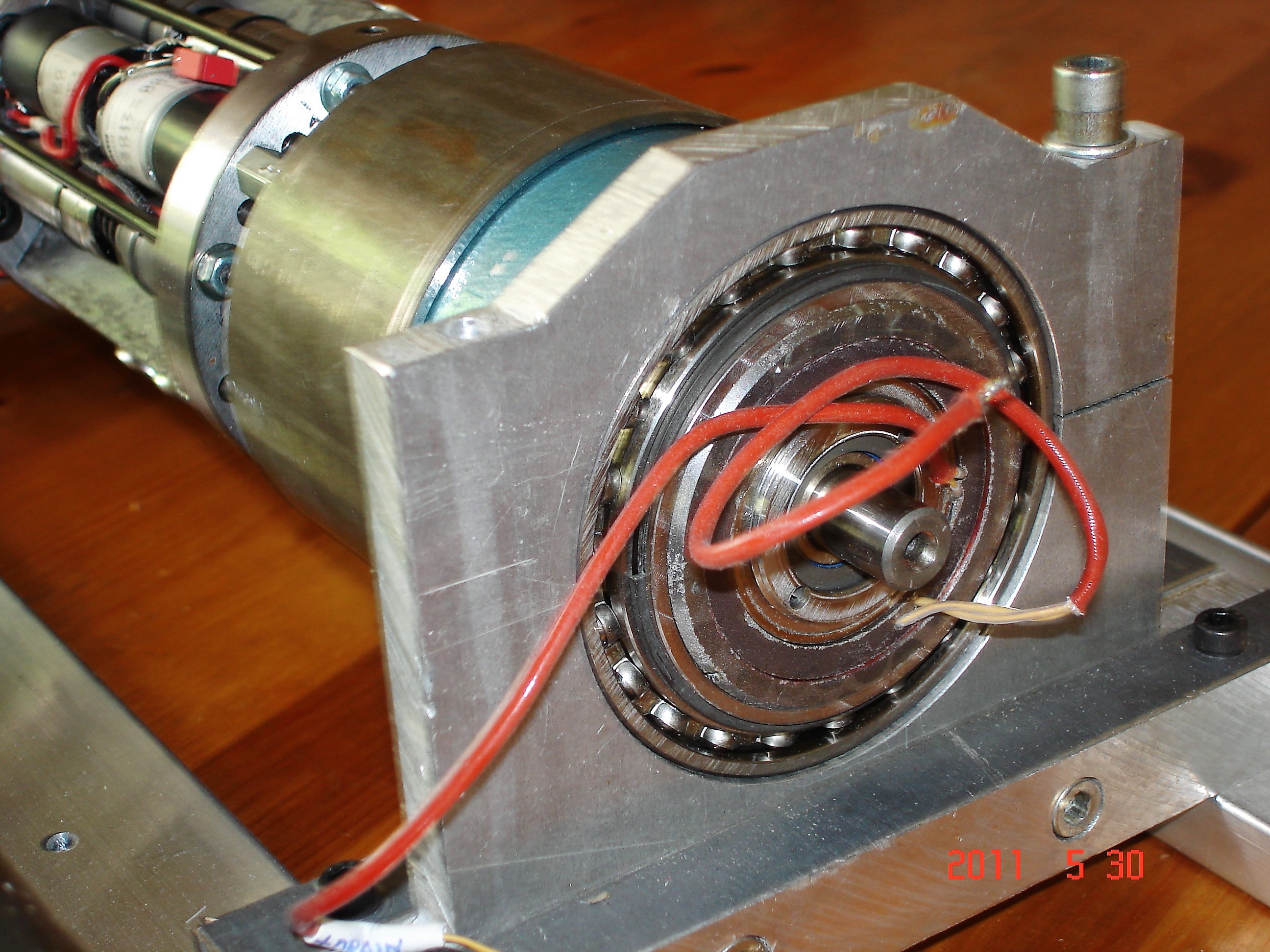
At each end of a shaft/rotor a hydraulic pump/motor with variable displacement are connected back to back and can pump towards each other and can work individually together as a rotating shaft in an electrical stator , the stationary part of a rotary system
No losses when driving straight than in a conventional drive train with differential, ratio 1:1
In a two wheel drive less power needed than with a two separate wheel motor allocation,when turning.
No extra weight at the wheels
Individual torque control
Suitable for Reluctance drive
A compact integrated drivetrain
The idea is patented in the United States and several European countries.
The implementation of the idea has been simulated by Linköping University.
What happens if you let two hydraulic pumps/motors with variable-displacement which are connected back to back pump towards each other and on the other hand work together and each of them with different displacement and the whole device in addition is rotating?
In the first case with equal displacement it will act as a rigid shaft without any losses and in the second case not with equal displacement as an rotating device it will offer different torque at the shafts. How does it look like and what will we get out of it?ith equal displacement
The answer of how the concept looks like and what we can get out of the concept follow below.
It looks like this.
It consists of a hydrostatic transmission formed as a shaft/rotor of axially (rotary) symmetry where the ingoing/outgoing shafts of the two hydraulic axial pumps/motors with variable-displacement also are the ends of the shaft/rotor of axially (rotary) symmetry, see enclosed photos. The two hydraulic axial pumps/motors with variable- displacement has the inlet and outlet from one pump/motor connected to the inlet and outlet of the other pump/motor and between are all auxiliary components, all included in a single housing.
The shaft/rotor can either from outside get power (torque x velocity speed) or leave power via v-belt drive or a traditional mechanical transmission indirect via an motor or generator or direct as a rotor in an electrical motor or generator. Outside the shaft/rotor there is a controller to regulate the total in or out coming power as well as control the split of its in or out coming power to the two shafts in different ratio of torque and velocity speed and direction of the torque between the two shafts or in the opposite way take care of the power in to one or of the two shafts of the shaft/rotor. It’s more explained in the enclosed Notes (not published on this website).
The control is done by controlling the displacement of hydraulic axial pumps/motors and the direction of the flow direction. The control and necessary power transmission inside and to the shaft/rotor are done by pulse modulation and voltage control in by a voltage regulator. The control from outside into the shaft/rotor is done by pulse modulating a DC feed current either mechanically via one or two commutators or inductively via one or two fixed coils concentric to one or two second coils fixed at one end or at each ends of the housings to the rotor. In a similar way as an electrical tooth brush is charged. The pulses which are coming in control separate servo systems which control the displacement of the pump/motor, where each one control a pump/motor of its own. The amplitude of the voltage regulators can control the direction of the flow by a valve and start a separate charge pump inside or just one of them if only one voltage regulator is used. The power is coming via the pulse modulated DC feed current mentioned above.
What will you get from the invention?. In a vehicle there is an extra demand for torque from one wheel of the shaft in a bent, and also to compensate for a skip or skid to keep the speed constant. Today the technique to control the out coming torque on the wheels is via one motor and differential or by a motor at each end of the shaft or via an extra mechanical transmission and an extra electrical motor (Haldex has shown a concept like that.) The first method can’t do all and you will have transmission losses, and in some extent you will need a diff- brake to solve a part of it. The second one the technique with a 2- wheel motor system, a motor and control system at each end of the shaft had to have an over “powered” motors not to slow down in the bent in comparison with a one motor concept via a differential. The power of the one motor will be twice the power of the motors in the 2- wheel motor system, but not with their over “power”. The third one with an extra mechanical transmission and an extra electrical motor will manage all.
The suggested concept by controlling the torque to the shafts/wheels will manage the extra demand for torque but with one motor at a power of two not over “powered” motors and integrated in one unit and probably not so heavy particularly not at the wheels and with no mechanical/hydraulic transmission losses when going straight forward. The efficiency when it’s not going straight forward will be 0.80 -0.85, so a fraction of it. Another example will be this. In a wind mill there is a need to control the rpm of the generator to be as constant as possible and not let the rpm of the propeller shaft get to high when it’ s too windy. There is probable also an advantage with low weight and few units when you assemble up in the tower. The suggested concept will be a solution to these demands in a design where you control the torque ratio between the ingoing torque at the ingoing shaft at one end of the rotating transmission, the propeller side and the torque to the shaft/rotor to or in a generator. The second outgoing shaft of the rotating transmission is here locked (fixed). It’s more explained in the enclosed Notes (not puplished on this website).
It means you can increase the torque the propeller has to overcome when it’s more windy. This design is more or less like a traditional hydrostatic transmission, the propeller is driving a pump with variable displacement which interacts with a hydraulic motor which drives a generator. The difference is... it is integrated in a rotor and probably not so heavy and spacious. The efficiency will be around 0.80 -0.85.
The transmission will have a continuous gear ratio, step less, unlimited in gearing down the number of revolution of the propeller and to gear up it will be limited to 1 to 2.5. The efficiency will be around 0.80 to 0.85 if you don’t need to gear up or down more. Then you will need a mechanical gearbox. Finally, another example, where the regulating and controlling concept of one motor with two outgoing shafts motor concept would be interesting is in different mills, for example in a crushing mill. As mentioned earlier with the concept used for vehicles the suggested concept can control/split the incoming torque in different ratio to the two outgoing shaft. Here you need two rolls rotate with different speed. The design could be that each one of the outgoing ends of shaft/rotor drives each one of the rolls, instead of using to separate drive lines.
72220
Västerås
Sweden